Here’s a simple truth: Making high-tech devices affordable, portable, durable, and mass-producible isn’t easy—especially if you also include profitable, a.k.a. not going out of business in the process. The design, engineering, and manufacturing challenges for the OEMs who make your favorite devices are real, and they are not trivial.
And lo, adhesives—inexpensive, versatile, and available in thousands of varieties from companies like 3M and Tesa—can neatly solve a lot of those challenges. So it’s not surprising that adhesives have proliferated in the innards of modern consumer electronics.
When it comes to repairability though, we adhere to some simple truths of our own. Ease of disassembly is king. Modular components rule. And that means adhesives tend to be really problematic for repair.

In other words, adhesives present many opportunities for straightforward and well-intentioned problem-solving by OEMs, but with major ramifications all down the line for end users, refurbishers, repairers, and recyclers—long after the warranty expires. You might say the question of whether adhesive is good or bad depends on your time horizon. Since repair is about longevity—another word for sustainability—we’re always trying to help OEMs lengthen their time horizon when making important design decisions.
And there’s never been a better time to re-evaluate the role of adhesive. At the moment, complying with Right to Repair legislation means OEMs merely have to supply things like replacement parts and service manuals for existing products, without rethinking product design—but the situation is evolving quickly. Repairable product design requirements (like user-replaceable batteries) are almost certainly coming soon to a major market near you. So OEMs that want to get ahead of the curve are already exploring more repairable solutions that are less reliant on adhesives.
Adhesive: What is it Good For?
Look, we get it—adhesive has lots of advantages.
It’s often cheaper, faster, and easier to assemble a product using adhesives, rather than screws or other reusable fasteners. Modern pressure-sensitive adhesives (or PSAs) bond to all kinds of material surfaces almost instantly—and unlike liquid chemical glues, they require no curing time.
PSAs typically come in the form of a tape, with a peel-away liner and backing, which can be inexpensively die cut into pretty much any shape you want. (Like crop circles, some of these have grown impressively complex.)
PSAs also take up very little space, so they’re extra handy for space-constrained products like mobile electronics and wearables. When portability and battery life are paramount, every bit of space saved is a win.
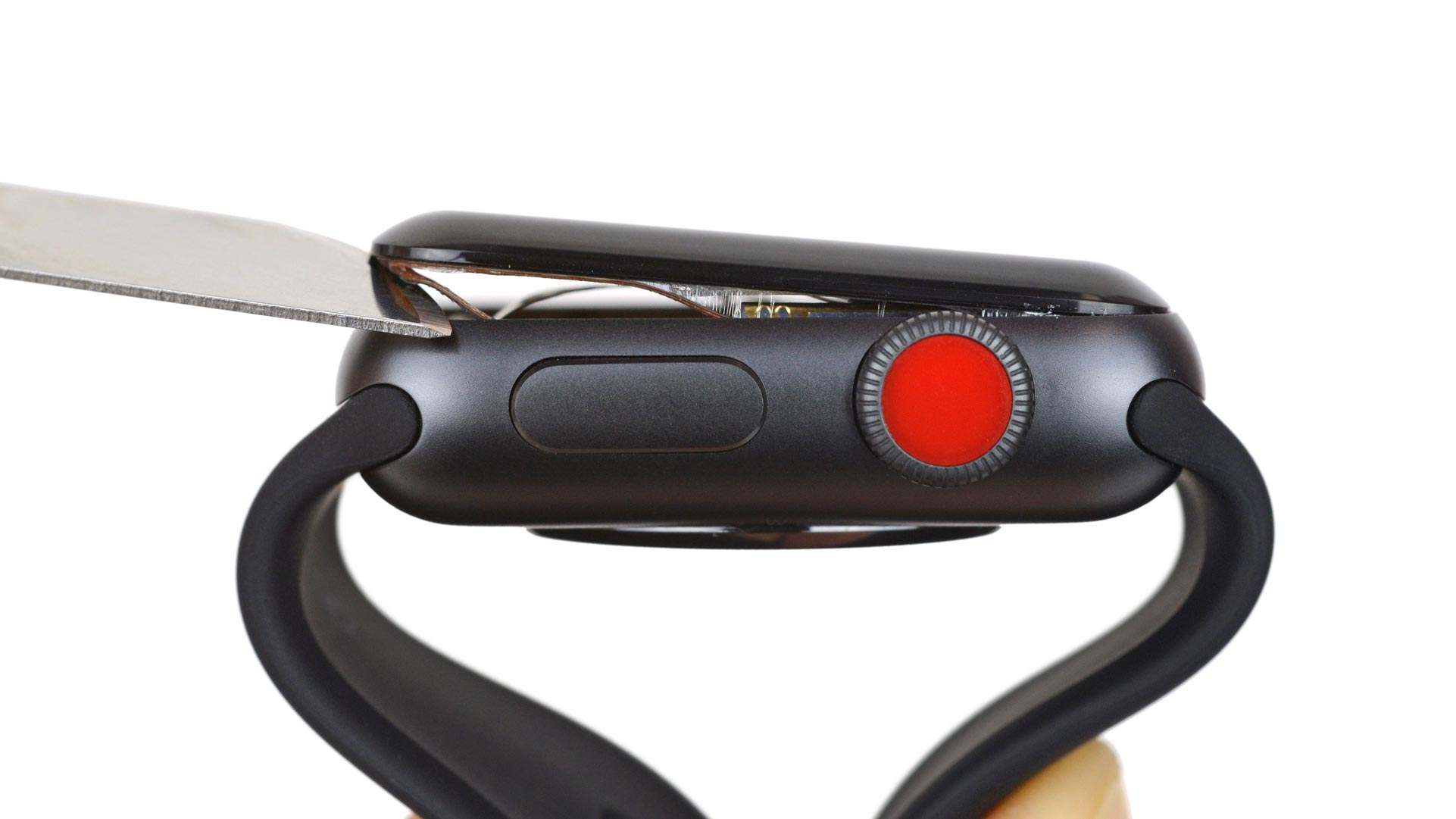
Many adhesives even serve multiple purposes. They’re commonly used to seal off your devices from the elements, protecting against liquid and/or dust intrusion. They provide cushioning for certain components, like the large glass panels on smartphones—there’s enough squish in the adhesive that a drop on the corner of the frame doesn’t transfer its entire load to the glass. They may also increase structural rigidity, for example by laminating a battery against the back cover of a tablet so it can more readily survive an accidental (or not-so-accidental) bend test.
These advantages are not trivial. Reducing reliance on adhesive is a serious design challenge for many OEMs.
What is it Not Good For?
Unfortunately, the convenience of sticking things together with adhesive tends to come at the expense of anybody who needs to un-stick them later. Troubleshooting, rework, refurbishing, repair, parts harvesting, and recycling are greatly complicated by over-reliance on adhesive in product design. In many cases, these efforts become completely impractical or uneconomical.
Why? One of the hallmarks of repairable product design is ease of disassembly—that is, taking things apart should be straightforward, nondestructive, and reversible, using readily available tools.
Adhesive usually fails all of these tests.
Separating adhesives can be maddeningly difficult and error-prone. The process often requires specialized equipment, controlled temperatures, and practice to get right—many repair shops have to invest in an expensive and ever-growing array of programmable ovens, hot plates, freezers, suction devices, jigs, and presses just to get something like a smartphone or tablet open and closed reliably, before even attempting a repair. Small mistakes can lead to catastrophe—cracked glass, punctured batteries, mangled flex cables, and other collateral damage are all too common.
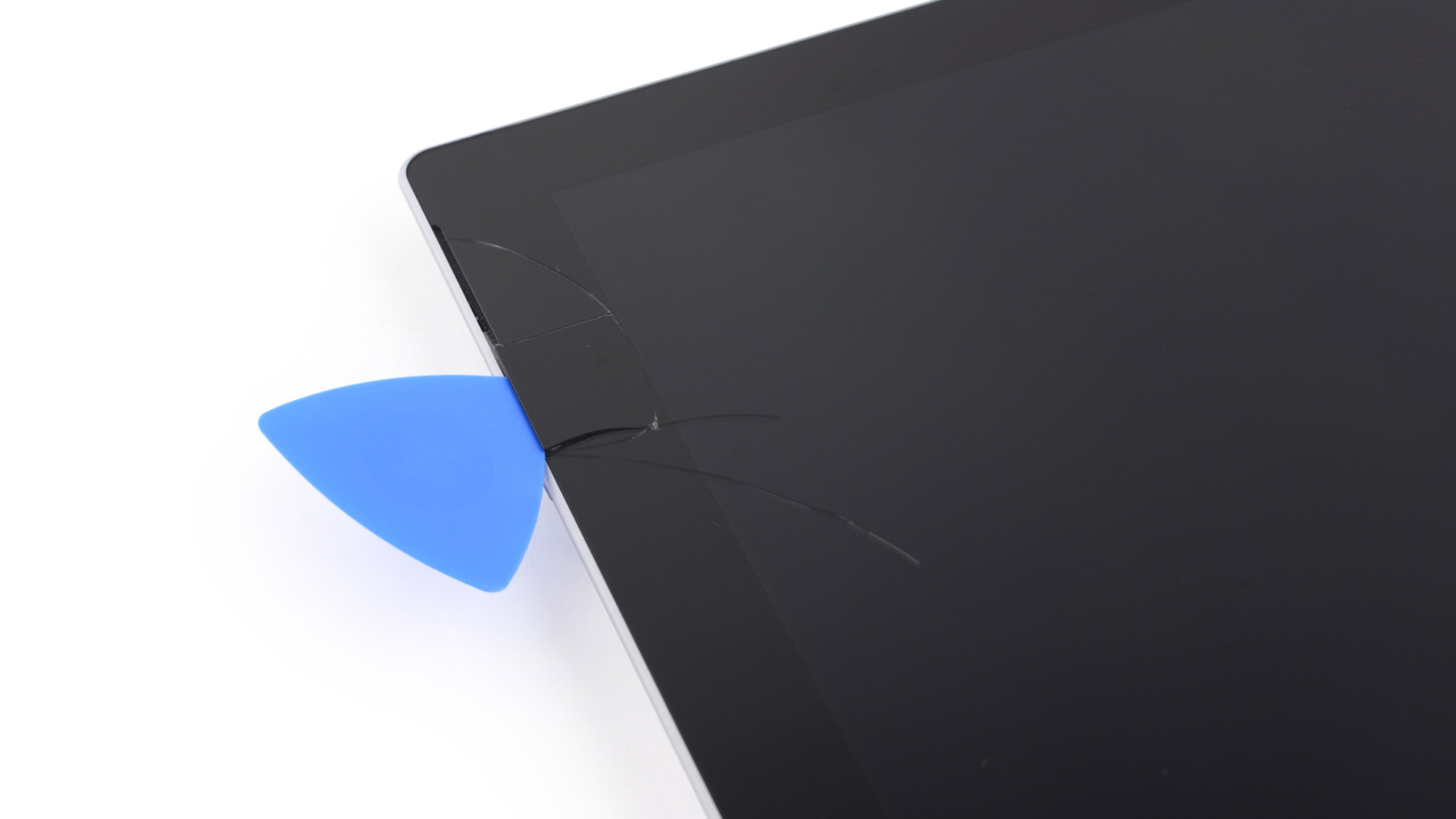
Once separated, the original adhesive can’t be reused—it must be painstakingly removed before thoroughly cleaning and prepping the underlying surfaces for fresh adhesive. This is another error-prone stage of the process, where an imperfect job can result in a poor bond (the device may not reliably stick back together).
And reassembly still may not be possible at all unless custom-cut replacement adhesives are available in abundance. Precisely positioning each tiny curve and cutout from a sheet of adhesive on the first try may be relatively easy in a manufacturing setting, but many ordinary humans are prone to messing this up. One tiny mistake, and you have to discard the adhesive and start over. When supplies run low, technicians sometimes resort to crudely cut alternative tapes or liquid glues that make any future repair/recycling attempt even more difficult.
Some of these issues have workarounds, but with tradeoffs in time and expense. Adhered-together devices can certainly be repaired; the question is whether anyone will go to the trouble.
Okay, What Are My Options?
In a word: innovate. To reduce reliance on adhesives, forward-thinking OEMs are already employing a variety of strategies that point the way to a more repairable future for our favorite electronic contraptions. These strategies can be loosely organized into the following three buckets.
Option 1: Choose a repair-friendly fastener (avoiding adhesives when possible). Screws, clips, magnets, snap-fits—anything that doesn’t hinder repeated disassembly/reassembly is a huge win for repairability over the adhered alternative. Where ingress protection is needed, sometimes a reusable rubber gasket or O-ring can suffice.
Admittedly, this can be the toughest option to implement. But this is also a space ripe for innovation, where getting creative will differentiate future products from the unsustainable, unrepairable competition of yesterday.
Among our favorite examples: Microsoft’s Surface Laptop. At launch, the first generation was impressively sleek and luxurious, but the adhered-together design made seemingly no concession to repair—we couldn’t find any way to take it apart without destroying it in the process. It netted a repairability score of 0/10, a first-and-worst-of-all-time for iFixit’s laptop rankings. Thankfully, the Surface team retooled the design, opting for strategically-placed magnets and screws under an adhesive-free lift-away cover—without compromising a single dimension of the original industrial design. Their hard work yielded the single biggest leap up our repairability scale ever, with the identical-looking but vastly-more-repairable Surface Laptop 3 netting a respectable 5/10. And the Surface team has continued to make steady improvements ever since—it just keeps getting better every year.
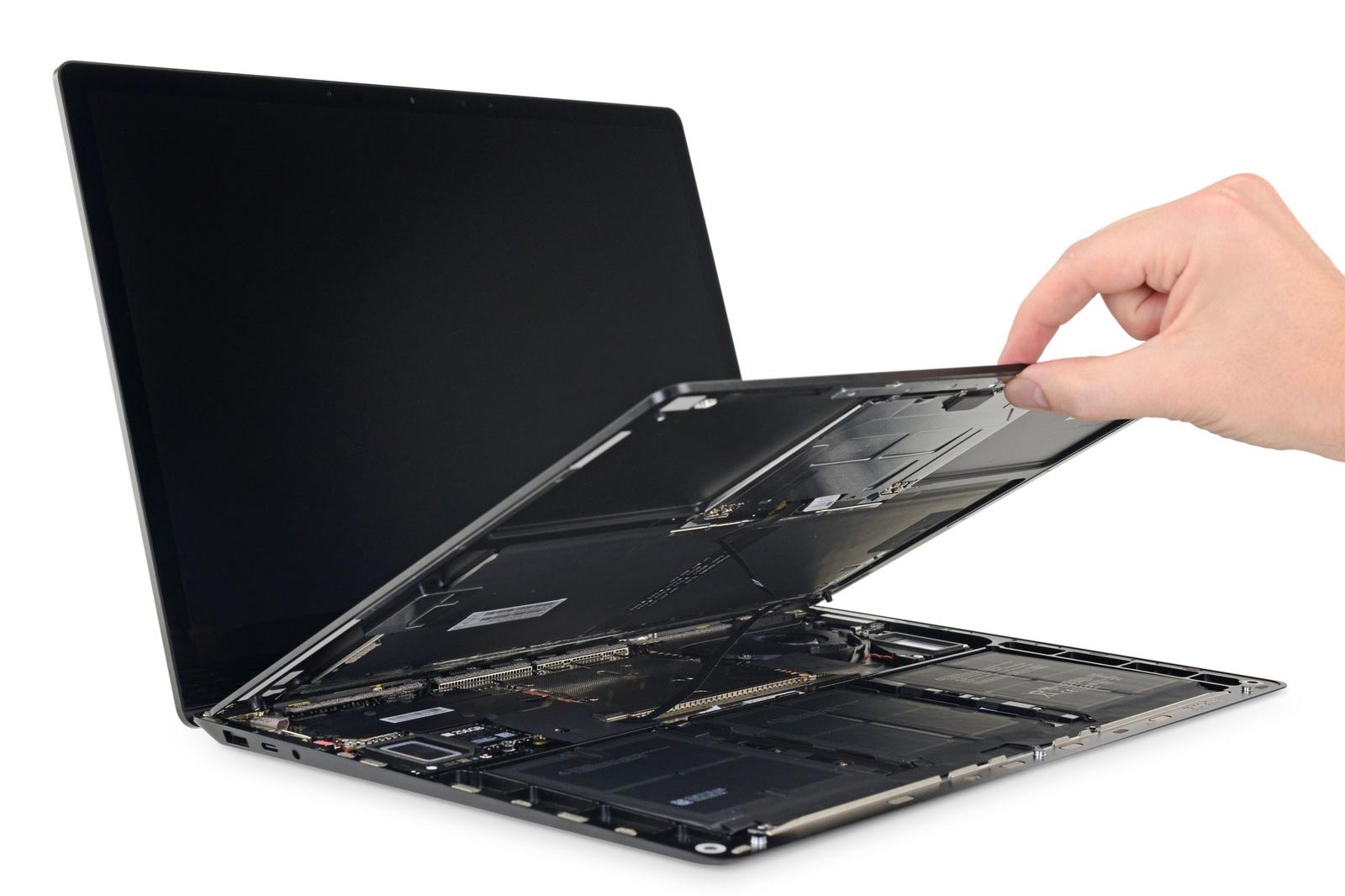
Smartphones present huge challenges for reducing reliance on adhesive, but here too we’ve seen encouraging progress. For example, speakers, charge ports, and sensors increasingly come with reusable waterproof gaskets rather than adhesives—speeding both disassembly and reassembly, and helping maintain ingress protection after a repair, all with less effort on the part of the repair tech.
How’s this for innovative: laptop display bezels are commonly adhered in place, but Framework fixed theirs with magnets and made it a user-customizable part. This takes repair a step further, opening up a potential new revenue stream and strengthening Framework’s connection with its customers by allowing them to personalize their product.
Even severely space-constrained devices like Bluetooth earbuds can be highly repairable if the adhesive isn’t overdone—some said it was impossible, but OEMs like Samsung and Fairphone stepped up and did it anyway.
The worst-case scenario is something like an iPad, or an early-model Surface Pro—fantastic products, darn near magical to use, but completely reliant on adhesive with almost no concession to repair at all. The screen, being the only point of entry, is adhered in place and a nightmare to remove (especially if it’s cracked). The battery is firmly glued in place, a huge problem for repair or recycling. Logic boards, cables, speakers—all adhered in place, each one a bigger hassle than the last. Happily, Microsoft has been hard at work on the problem, and current-model Surface Pros are vastly more repairable than their predecessors. We’re still hoping for similar improvements to the iPad line. (Apple is surely aware of the problem, having in recent years released repair parts and service manuals for iPhones and Macs—but to date, no hint of how to repair an iPad. The iPad could be Exhibit A for why parts and instructions aren’t much help if the product design isn’t repairable, and we’ll go out on a limb and say that over-reliance on adhesives is at the heart of the problem.)
Option 2: Provide reusable fasteners in addition to adhesive. Although this is an imperfect solution, it greatly alleviates the reversibility problem. That is, it helps if the device can be reliably reassembled regardless of the state of the adhesive. (When things are held together solely with adhesive, there is no margin for error—a mildly imperfect bond or scarcity of supplies can lead to disaster, putting the device out of commission indefinitely.)
Our favorite examples here come from the smartphone world, mainly iPhones and certain model Google Pixels. Their screens and/or back covers are still adhered in place (partly for ingress protection purposes), but they also secure with screws or clips. If you need to reassemble quickly to troubleshoot or test a repair, or if you mis-applied a replacement adhesive and need to wait for fresh supplies, it’s no problem. (We’d love to see this approach employed more universally in smartphones, smartwatches, or even iMacs—nobody likes completing a triumphant repair only to have something important fall off a day or two later.)
Option 3: Use the least problematic adhesives. Some adhesives are a bit more repair-friendly than others, mainly by virtue of being easier to disassemble. They still lack reversibility or reusability in most cases, which makes them less than ideal—but if adhesive is the only option, these help take the sting out of future repair efforts.
Stretch-release adhesives (a.k.a. bond-and-detach or “Command” strips) provide an opportunity for clean, low-force removal without fancy tools, controlled temperatures, or messy solvents. These are double-sided, high bond tapes that have become popular for mounting soft batteries. Simply pull to stretch it out, the bonding strength disappears, and the adhesive slips out as if by magic—the polymers used in the adhesive realign into long, skinny chains that lose their tack and slide right over surfaces that would normally grab.
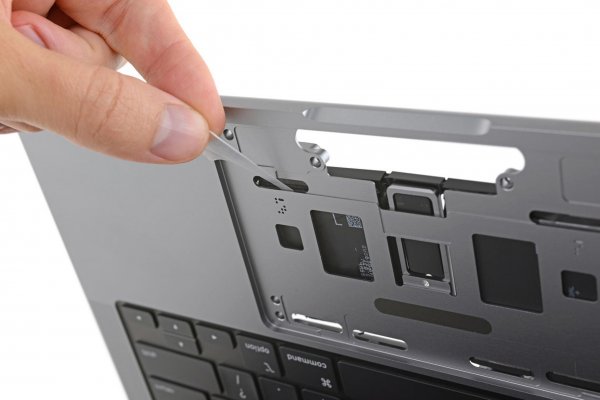
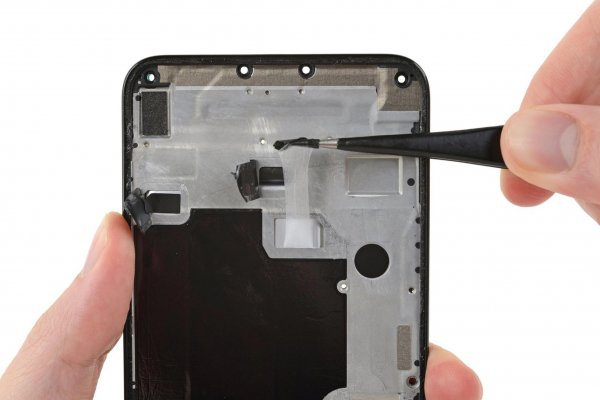
Two caveats here: one, the detaching technique takes practice and is far from foolproof. The strips must be pulled evenly, at a shallow angle, and without wrinkling, or they can easily snag and snap in half, forcing the would-be repair tech to fall back on solvents and pry tools just like a conventional adhesive. And second, these require some non-trivial design work on the part of the OEM—allowing for slightly more thickness than conventional tapes, as well as providing enough clearance to pull the strips out at a shallow angle, without snagging on adjacent components.
Other adhesives that separate without heat/solvents—We’ve seen adhesives that are mild enough to separate by hand using a built-in pull tab, greatly speeding disassembly. (Just make sure the pull tab is up to the job! Real-world tests don’t always match expectations.) It’s even better if these retain enough tack that they can be safely re-used. We’ve also seen adhesive strips with a foam core that’s easy to slice through at room temperature, and that peel away easily by hand with near-zero residue, such as on iMacs and late model Surface Pros. While this still isn’t an ideal or easily reversible solution, it speeds disassembly and cleanup a great deal vs. standard adhesives.
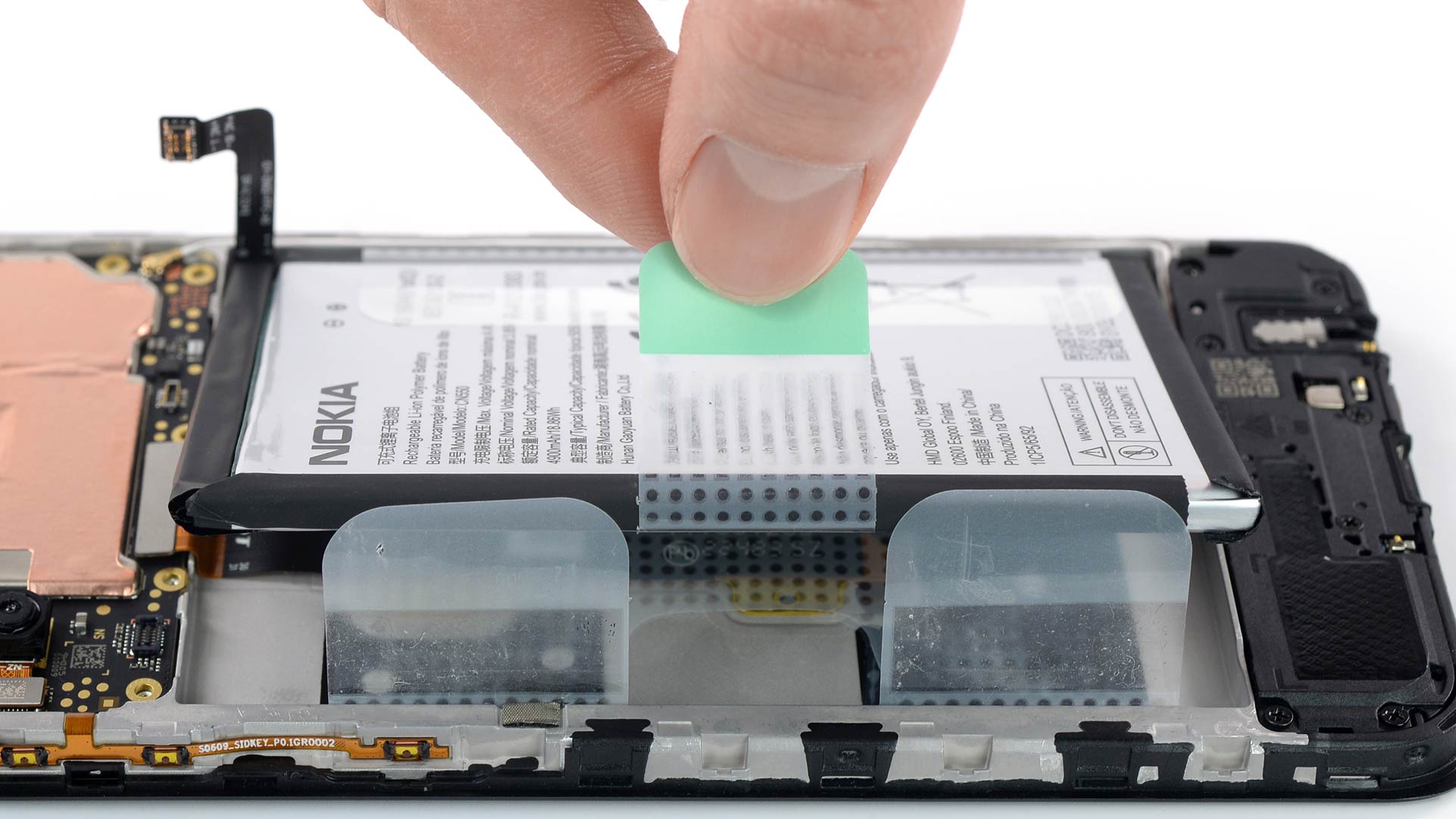
Option 4: Watch the competition. Fairphone, Framework, Lenovo, Microsoft, and other OEMs that we’re increasingly excited to talk about are embracing repairability and eschewing adhesives in a variety of intriguing ways. Not all innovation comes in the form of faster processors or better cameras; OEMs who want to rise above the competition can push the frontiers of repairability to make a superior product.
The Future is Coming Unglued
It’s surely challenging at times to design sleek, modern, affordable products while minimizing reliance on adhesives—but we think this is a design challenge that sets the best OEMs apart. Those who overcome the challenges and enhance repairability in creative ways have garnered glowing press and a rabid fan base, while those who refuse have attracted the attention of regulators. As more Right to Repair laws take effect in 2024 and beyond, OEMs that get ahead of the curve on repairability will likely find themselves at an increasing advantage. Those that don’t … may find themselves stuck.
Один комментарий
also: please don't hide screws under adhesive attached stuff (padding feet, etc)
Edho Arief - Ответить